115 Main St
We purchased this property back in 2016 with the intention of renting out commercial space. It was my wife’s grandfathers video store for decades before he passed away. It had a tenant when we bought it but the building needed some work.
Property at purchase in 2016
The margins on this were pretty thin so we fixed it up as economically as possible.
I had no idea what I was doing so I sought advise from some local and seasoned real estate agents and they all felt confident things would go well. I did the math and I needed get at least $.67/sqft which seemed reasonable. This is less than half of similar places in Omaha and surrounding areas. At that time there were no other commercial spaces for rent on Main Street so I felt confident it would be easy to rent. What I didn’t realize is how different residential and commercial properties are. What was surely good advise for residential turned out to be bad advise for commercial. Long story short it sat vacant for nearly 2 years. We hired a broker, thought of starting our own business in it but nothing was economically feasible. It was looking like we either had to sell it for a loss or find a way to justify fixing it up.
Renovations
One consistent concern with perspective tenants was finding living space in Louisville. This stuck in my mind and I started to think about adding an apartment to the building. I checked with the city and as long as the living quarters are on the 2nd story there wouldn’t be any issues. I fired up AutoCad and cranked out some 2D drawings and started playing with the numbers.
Draft building concepts
I played around with the concept of creating a 2nd floor for the entire existing building and have 2 apartments. Summer 2018 we decided to sell our house in Louisville and use the cash to build the apartment on the building. We planned to live there for 2-5 years then either rent it or sell it. Molly had to move to Ames, IA for the last 2 years of her veterinary school and this seemed like the perfect time for me to go into “bachelor mode” and pump this thing out. Come June 2019 we were moved out of the old house and I was 100% committed to finishing the building. I started ordering materials the first week of September 2019 and I started demolition the following week. The planned called for the entire west most structure to come down. It was in bad shape from water and termite damage. The north side of the building is from 1998 and made from 8″ cement block. The southside is the oldest part of the building. I don’t know the exact date but it was sometime in the fourth quarter of the 19th century. The walls are thick and made from sandstone. They are widest at the bottom and taper toward the top. The below picture is about 5′ from the top of the wall and it’s nearly 2′ thick. There are several old roofs on that building and it’s had a lot of cobbling over the years and it was wasn’t pretty but it was in good structural condition.
Thick sandstone walls
I went hunting for historical pictures of the building but I was only able to find two.
Buttercup Cafe 1969 Left, Flood of 1923 Right
Back up a bit
I realize this jumps around in time but bear with me. I had the footings dug and poured and we finished the block foundation for the new building in December 2017. At the same time I started to demo the inside of the structure that would eventually come down. Dad was of course there to help me lay the block. (L250 demolition mode enabled!)
In July of 2019 I decided to install a roll up garage door so it would be easier to store materials. Dad was of course there to help me.
Demolition
Fast forward to September 2019 and we are ready to tear it down. Unfortunately the foundation acted as fish bowl and with the gutters torn off the old building it flood every time it rained.
Muddy Mess!
I was waiting for the cooler temperatures of fall before I started. We had an especially hot and rainy summer but I was counting on a cool and dry fall. I started demo on September 21, 2019. The Lull and L250 were there to help.
In case I don’t say it enough I had a lot of help on this project. Jason, Markus, Kyle, Jake, Mark, Shari, Katie, and especially my father in law Terry and my dad Dan and my brother Eric. Last but not least my lovely wife Molly who wasn’t physically there but had to put up with my all of my insanity while working 12 hour night shifts in the ER.
Video of the structure coming down
First Floor
The first wall went up on October 9, 2019. The plan for all of the construction was to build the walls on the ground then use the Lull and L250 to stand them up into place. Steps for the walls:
- Frame it
- Sheet it
- Wrap it
- Tin it
- Stand it up
- Repeat
The bottom 4′ of the south wall was made from poured concrete. Unlike the concrete block that used to sit atop it the wall was in good shape. I had planned to remove it but we started to worry that doing so may damage the legion building. The only way to do it would be to tear up the concrete pad and dig the wall out away from the Legion but the pad was in good shape and I had planned to keep it. Tearing it out would be extra cost and setback in time so I decided to use it and move forward.
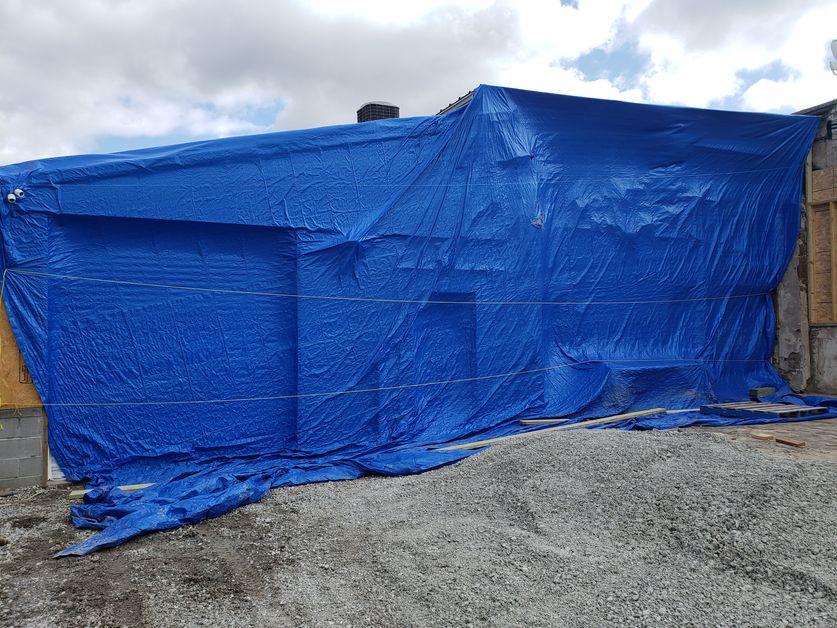
If I was there Neelix was there. He has this way of laying in unnatural contorted positions that always freaks me out thinking I ran him over.
My brother Eric volunteered to come up from Florida and help me. He arrived on October 19, 2019 and left October 29, 2019. We barely stopped working the entire time he was there. We would work to about 1am then start again in the morning. It’s safe to say I wouldn’t have completed this if it weren’t for his help. When he got there I had two walls up on the first floor and by the time he left 10 days later we were putting the roof on.
When Eric Arrived and when Eric Left 10 days later
More pictures of the first floor construction:
By the end of the following afternoon we had the sheeting laid for the second floor.
Next up, walls. The second floor walls were going to be tricky. We couldn’t go on to the neighbors property so it had to go up as a completed wall but it was too far for the Lull to reach. L250 to the rescue. I took the bucket extender off and used the Lull to rest it on the second floor. From the crane scale measurements I know it weights about 2000lb which is well within the capacity of the floor joists. The L250 made short work of lifting the walls.
By the end of the day on October 27, 2019 all 4 walls were up on the second floor. Next up, trusses. These are 48′ long and weight over 300lbs. On the 28th we started lifting the trusses on the roof. I pre-sheeted and wrapped the end trusses but I couldn’t tin them as that needed to be done after the everything was up.
It was now November 1st and Eric was back in Florida but my father in law and nephew helped me finish the roof. Dad also came by and decided to used my preferred method of reaching the second floor, the Lull ladder.
By November 3, 2019 the roof was done. Neelix taught me that sometimes you have to stop and enjoy the music.
In the moment it seems like you’re taking pictures and videos constantly but looking back I always seem to take too many pictures of the details and miss the big picture. Luckily I caught a few moments.
Setting the first trusses
Next I had to install the soffit on the north side roof overhang. Again I couldn’t go into the neighbors property so I had to find a way to lift myself 25′ in the air and reach out 34′. I ended up making a 34′ long 4′ wide plank for the Lull using the 12′ fork extenders as a base with 2×6 framing under 3/4″ plywood.
The main goal was to get the building sealed up before winter hit in full force and by this point I had achieved it. I still had to finish the siding on the outside but it was good enough to work inside on the cold days and pick away at the exterior when the weather was cooperating. Next up, 2nd floor interior walls. Terry was again a great help. This is by far the biggest construction project I’ve ever taken on and I welcomed any experience or wisdom he had to offer. During this time Molly was in Ames, IA and I really needed her help to nail down the final floor plan. While she was working nights in the ER I was texting her pictures of wall layouts or the position of the bathroom fixtures.
Interior 2nd Floor Framing
At the time I thought I jumped the gun ordering drywall. It was delivered on December 2, 2019 but I wasn’t ready for the drywall guys until early January. So for about a month it was a giant thing in the way but in the end it all worked out. I thought for sure the drywall was going to snap in half when the delivery driver was unloading it. I never knew drywall could flex that much.
Drywall Delivery
I took every opportunity with good weather and had the exterior finished by December 5, 2019.
Electrical
One benefit of having a commercial property is I can get 3 phase power. The downside is you are required to use a licensed electrician for the commercial portion of the building but it all ended up working out in the end.
New 3 Phase Power
The rest of the electrical was uneventful except for maybe going a little overboard with layout and labeling. Ron made that little holder for the wire spool which I still have to this day.
u start to do weird things working like this.
During this time the transmission blew in the truck (which I used everyday) and Dad nearly died from a virus. One bucket contains burned transmission fluid, the other is blood from dad’s lungs.
Molly got in an accident in Des Moines, IA leaving the zoo where she was working for school. Some old lady ran into her driver side rear tire and bent the control arm and shock. I ordered her an Uber to get her home then I dropped what I was doing and headed out. It was about 8pm when I left and luckily I was able to find a parts store with the parts before leaving Omaha. I found her car in the parking lot around 11pm and started working on it. Lucky for me I was able to fix it there and we came back the next day and got it.
The van is 15 years old with nearly 1/4 million miles on it but it was a trooper. Those are 2x12x24′ strapped to the roof. Don’t get me started on why I love minivans.
Enough side tracking let’s get back to the construction.
Insulation
The walls are 2×6″ which is 50% thicker than a standard house wall. Menards had a sale on insulation in November so I took the opportunity to buy it but again I had to store a massive pile of materials.
Highspeed video of my mother and father in law helping me cut and hang insulation.
Where are we at? It was January 19, 2020. I was nearly completed with the insulation and the drywallers were supposed to come the next day but showed up early. They said don’t worry they won’t be done before you finish but let me tell you those little 95lb 4’8″ tall Guatemalans could sling some rocks. They had the entire second floor done in a day and were on my heals as I finished the insulation downstairs. Unfortunately I had to leave town for work and I had to move out of the house I was staying in before I left so it was a mad rush to get everything done. Ron helped me move the furniture out and I just pilled it up downstairs and planned to worry about it when I got back. Mind you I have no working shower so that took priority when I got back.
My body was pissed and everything hurt so the first few days of the work trip felt great. I was gone for about 2 weeks and by the time I got back the drywall was done and there was a coat of primer on the second floor. I was planning to do the painting myself, I bought a nicer Graco airless sprayer that I used on the old house and I bought some extension poles so I could reach the tall ceilings. I suited up and tried painting for about 10 minutes but it was awful so I gave up and hired one of the guys who was doing the drywall to paint the first and second floors.
More to come…